Global Elites with Sparkling Smart Wisdom Gathering At “2018 Supply Chain & Logistics Inno
Maitrox - Experience Sharing of “The Innovation and Promotion of After-Sales Service Model Driven by Smart Supply Chain”
“More than 500 global participants attended ‘2018 Supply Chain & Logistics Innovation Summit’. Over 20 speakers made brilliant speeches on the summit. Yao Fang, the vice president of Maitrox , shared the practices of smart supply chain.”
“2018 Supply Chain & Logistics Innovation Summit” was held in Shanghai from May 24th to May 25th. The summit included the supply chain innovation forum and the logistics innovation forum. Under the background of global vision, global supply chain experts discussed the supply chain opportunities of China; meanwhile, they were devoted to explore the future supply chain driven by clients and technology. This was a grand annual event for supply chain industry.
Maitrox was invited to attend the summit and our vice president, Yao Fang gave the speech of “The Innovation and Promotion of After-Sales Service Model Driven by Smart Supply Chain” for the audience. During the speech, Yao Fang took India and Thailand as examples, and shared our practical experience of local after-sales supply chain. We helped our clients to optimize their oversea after-sales service models, promote “One-Hour Quick Repair”, and improve the service quality and brand reputation.
With the era of economic transformation, and industrial integration and promotion, the growth of sales for Chinese companies has encountered to a new period of bottlenecks. Thousands of companies have begun to reexamine the traditional way of sales, and they have sought to complete the supply chain revolution in a new way. In this supply chain revolution, Chinese companies have gradually realized that products sold to the customers is no longer the end of the supply chain, but the new start. The values created by after-sales service have become more and more important. The value-added service which is focused on “service” itself will become a new growing point for the performance of all Chinese companies.
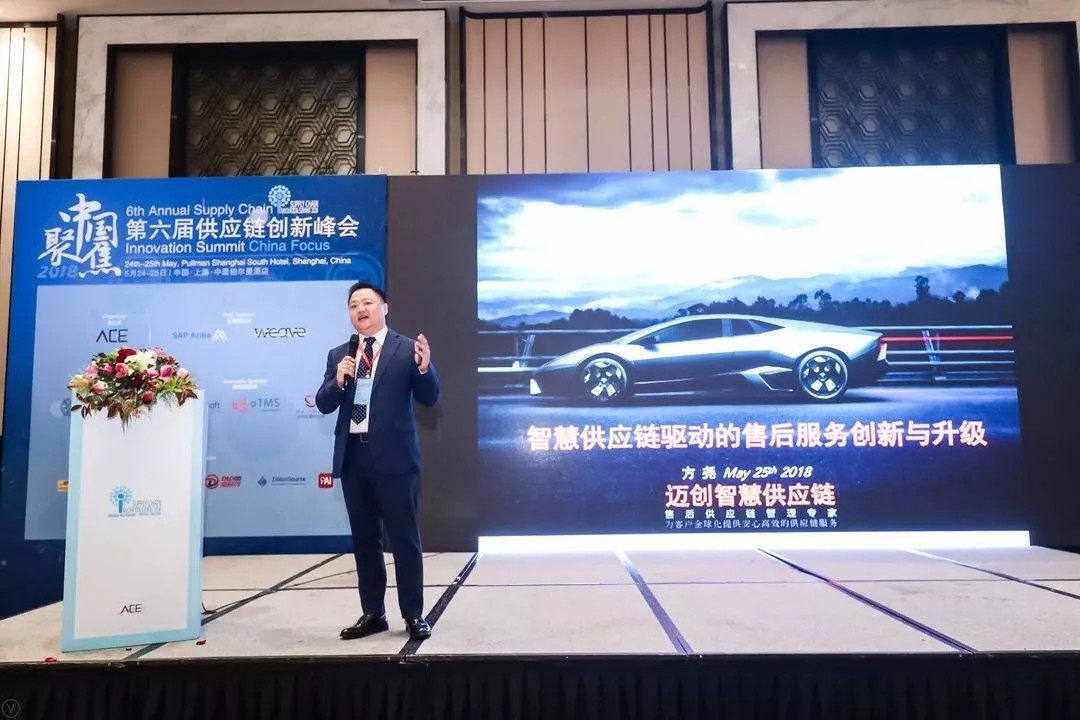
As the pioneer of after-sales supply chain service for Chinese brands going
overseas, Maitrox found the values for the growth of company
performance through improving the supply chain based on the internet a few years
ago. Maitrox starts to provide the oversea after-sales supply chain service of
electronic products, and present the new service idea of “One-Hour Quick
Repair”. Through years of innovative exploration, Maitrox’s after-sales supply
chain management services with the purpose of reducing cost and improving
efficiency has already served many Top 500 worldwide clients and national
brands, and has become a good helper for them in after-sales service area.
The innovative service of “One-Hour Quick Repair” has integrated three models of“PPU+PUSH+DESC” in order to help mobile phone brands accurately forecast the number of spare parts they need. Maitrox would first buy spare parts, then set up warehouses covering the nearby distance of maintenance sites for storing these spare parts, forecast the number of spare parts according to the estimation of big data, and finally send spare parts to the warehouses nearby the maintenance sites. This ensures that “spare parts on hands, no worries of repair”. As long as the customers go to repair their phones and spare parts are used along with the repair orders, mobile phone brands then pay the service management fees for Maitrox according to the number of repair orders. At the same time, these authorized maintenance sites have the functions of “mobile phone maintenance service center” and “spare parts distribution”. They make “DC”(Distribution Center) and “ESC”(Exclusive Service Center) into “DESC” so as to achieve the goals of “maintenance”, “distribution”, and “shared inventory”.
On the Summit, Yao Fang also shared the case of Indian after-sales supply chain solution. There used to be a customer who brought his own products and went to India. Once the products were sold within India, they ranked No.2 on the sales list in India. And then he opened more than 500 maintenance centers in India as well. However, the ideality was full, the reality was cruel. There were continuous problems such as PAL (parts available level) was low (0BD 65%,3BD 80%); the inventory TAT (turnaround time) was long (5 months); lots of fake orders; bad spare parts returning period was long; and lacking of materials as well as redundancy happened. Maitrox provided the customer with a comprehensive supply chain solution according to these tough problems. We had unified the demand forecast of after-sales service spare parts in India. We had upgraded qualified ESC to D-ESC. We assisted the distribution in regional markets and we did bad spare parts return together. We used our smart system to plan for after-sales material planning and distribution. We ensured that the KPI of material could be achieved.
Maitrox helps customers:
Efficiently changed the layout from ASP into D-ESC within 3 months; 3 ASPs had been increased to 50+ D-ESC; the time of spare parts supply and bad spare parts turn was significantly reduced;
The average PAL of 0BD was increased from 65% to 93%, and the average PAL of 3BD was increased from 80% to 96%;
The inventory TAT was reduced from 5 months to 3 months;
The overall after-sales costs were greatly reduced;
Indian after-sales business ranked No.1 worldwide in the after-sales performance within the Group evaluation.
The “One-Hour Quick Repair” of Maitrox Smart Supply Chain can be achieved by integrative smart planning system. It can correct the mistakes immediately, do precise forecast, reduce the inventory, reduce the frequency of logistics, reduce the number of management staff, and finally achieve collaborative and systematic management of high-level repair.
The new ground of “One-Hour Quick Repair” explored by Maitrox is the new model for the development of electronics products after-sales supply chain. In the future, we will provide the global after-sales spare parts solutions for large clients, the global after-sales spare parts elite solution (One-Hour Quick Repair), the global after-sales solution for the small and medium clients, the after-sales POD solution for large clients, the VMI/JIT inventory solution in the production line for large clients, the global spare parts rebalance for large clients, mobile/computer industrial solutions, automotive industrial solutions, household electronic appliances industrial solutions, and so on. We also have reasons to believe that today’s market with digitization and information, Maitrox can provide good and advanced service to help our clients completely change in a brand new way based on our 14-year experience. We can finally help them to lead in the domestic supply chain service market
Introduction of “2018 Supply Chain & Logistics Innovation Summit”
As the foremost supply chain summit, more than 500 global senior business representatives were invited to attend “2018 Supply Chain & Logistics Innovation Summit”, and more than 20 supply chain executives and experts shared their best practices of supply chain, supply chain innovation, technological change, supply chain network optimization, procurement, and so on. The in-depth discussion lasted for two days. The summit aims to build a platform for supply chain business cooperation and communication within supply chain industry. Participating companies come from Global Top 500 companies in the industries of manufacturing, FMCG, retail, e-commerce, pharmaceuticals, high-tech; Chinese Top 100 companies, and other global well-known service companies providing logistics, warehousing, software, and supply chain solutions.